Designing a laboratory is a complex process that requires careful planning to ensure efficiency, safety, and compliance with industry regulations. Whether designing a new facility or refurbishing an existing space, getting the lab layout and space allocation right is crucial for productivity and research integrity. This guide explores the key considerations for laboratory space planning, layout design, and best practices for maximising functionality.
Key Space Requirements and Regulatory Guidelines for Laboratories
Laboratories must be designed with specific space allocations in mind to meet operational and safety needs. Fortunately, there are established benchmarks and requirements for laboratory space planning, so you can feel confident in the safe and optimal running of your lab space.
Lab Space Requirements Per Person
The amount of space required per laboratory worker depends on the type of research and activities being conducted. Laboratories must balance efficiency with safety so that personnel have adequate room to work comfortably while maintaining compliance with health and safety regulations.
- General Research Laboratories: Typically, 10-15 square metres per person is recommended to allow ample space for workstations, equipment, and movement.
- Clinical Laboratories: These require slightly more space, around 15-20 square metres per person, due to the specialised equipment and safety measures necessary for handling biological samples and medical tests.
- Specialised Laboratories (e.g., biosafety level 3 or 4): For high-risk environments, such as pathogen research labs, 20+ square metres per person is often required to accommodate strict biosafety protocols and containment facilities.
Regulatory Considerations
Designing a laboratory goes beyond functionality—it requires careful attention to regulatory standards that safeguard both people and scientific work. Compliance with national and international safety guidelines is essential for creating a secure and efficient environment. These regulations help prevent hazards, protect equipment, and maintain research integrity.
- Health and Safety Executive (HSE) Guidelines (UK): These guidelines outline workplace safety requirements, focusing on risk assessment, proper ventilation, and accident prevention measures to protect laboratory personnel.
- Building Regulations and British Standards (BS EN 12128:1998): This standard covers various aspects of laboratory construction, including ventilation, infrastructure integrity, and secure design criteria.
- Good Laboratory Practice (GLP): A global framework monitoring the quality and reliability of laboratory data. Adhering to GLP principles helps maintain compliance with industry regulations and research reproducibility.
- Fire Safety and Hazardous Materials Storage: Laboratories must follow fire safety codes for appropriately storing hazardous chemicals and materials. Proper emergency exits, fire suppression systems, and chemical containment solutions must be incorporated into the design.
What are the Main Approaches for Designing Laboratory Layouts?
Laboratory layout design is shaped by specific research needs and operational priorities. Different approaches support various workflows, safety requirements, and collaboration styles, influencing how efficiently a lab functions. The right layout can enhance productivity, streamline processes, and accommodate future growth.
Functional Layout
A functional laboratory layout divides the space into clearly defined zones, such as preparation areas, testing stations, storage rooms, and administrative offices. By grouping similar tasks together, this design minimises unnecessary movement, enhances workflow efficiency, and improves safety by keeping hazardous processes contained within designated areas. This structured approach is particularly beneficial for laboratories handling complex procedures, as it streamlines operations so that essential equipment and materials are always within reach.
Process-Based Layout
A process-based layout is particularly useful for laboratories involved in diagnostic testing and chemical processing because it organises workstations based on the sequence of operations. This minimises cross-contamination, improves workflow efficiency, and ensures a logical progression from sample preparation to analysis, reducing handling time and errors.
Open-Plan Layout
This setup promotes easy communication between researchers, making it ideal for multidisciplinary environments where teamwork and knowledge exchange are essential. By reducing partitioned areas, an open-plan layout also allows for greater flexibility in adapting the space to different projects or research needs. However, careful planning is required to manage noise levels and ensure designated zones for tasks requiring controlled conditions.
Modular Laboratory Layout
A modular laboratory layout offers a highly adaptable design, featuring movable workstations, reconfigurable furniture, and adjustable infrastructure. This approach allows laboratories to quickly adapt to evolving research requirements, new technologies, and changing team structures without the need for costly renovations. Ideal for dynamic research environments, modular layouts support future growth, enhance space utilisation, and can be customised for specialised equipment or workflows. Additionally, integrated utilities and flexible ventilation systems help accommodate a variety of scientific disciplines within the same space.
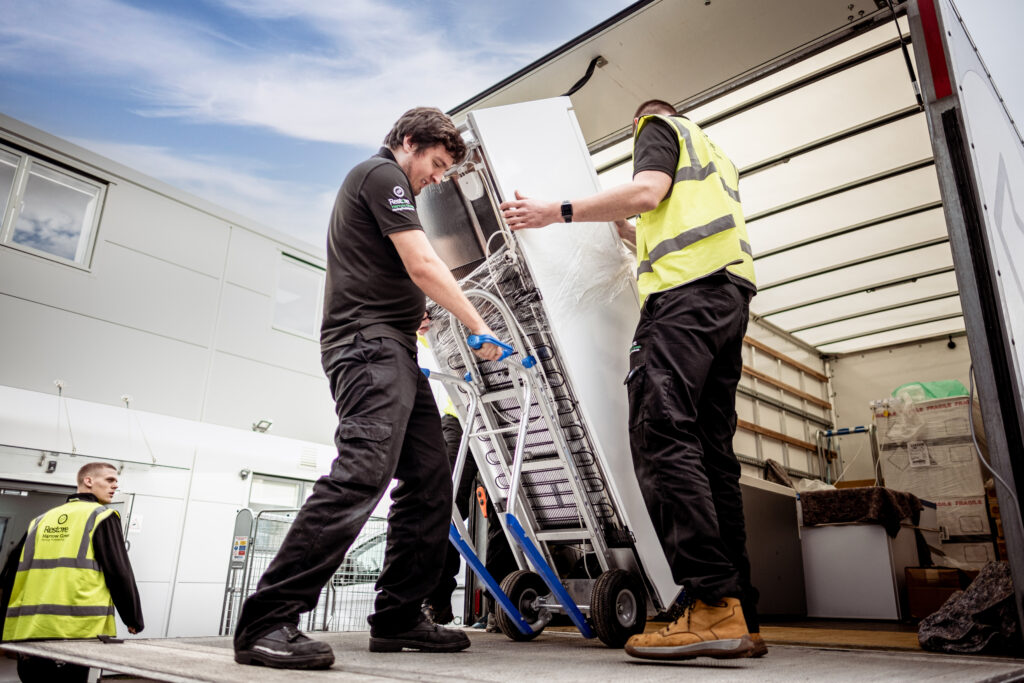
What are the Different Types of Laboratory Layouts?
Different laboratory layouts cater to specific research functions and industry needs. Each of these layouts integrates key principles of workflow efficiency, safety, and adaptability to meet the diverse needs of scientific research and industry applications. The most common types include:
- Analytical and Quality Control Laboratories: These labs focus on precise testing and measurements, requiring segregated areas for sample preparation, instrumentation, and data analysis.
- Clinical and Medical Laboratories: Designed for diagnostic testing and medical research, these labs require stringent biosafety measures and clearly defined work zones.
- Research and Development (R&D) Laboratories: These flexible spaces support innovation and product development, often incorporating both wet and dry lab areas.
- Teaching and Academic Laboratories: Used for educational purposes, these labs prioritise accessibility and structured workstations for students and faculty.
- Biosafety Laboratories (BSL-1 to BSL-4): These labs follow strict containment protocols for handling hazardous biological agents, with security measures increasing at higher biosafety levels.
Steps for Designing a Laboratory Layout
1. Define Space Requirements
Determining the appropriate space for a laboratory is crucial for smooth operations, safety, and efficiency. The space should accommodate personnel, equipment, and storage while allowing for future expansion. A well-planned laboratory considers the type of research conducted, the number of employees, and the workflow. Proper spacing allows researchers to move freely without unnecessary obstructions, reducing the risk of accidents. Moreover, laboratories should be designed with flexibility in mind to accommodate future technological advancements and new equipment.
2. Assess Workflow and Operations
Understanding the laboratory’s workflow helps in designing an optimal layout that enhances productivity and safety. The placement of workstations, equipment, and storage areas should align with the natural flow of activities to reduce unnecessary movement. Logical workflow patterns should be implemented to minimise contamination risks, particularly in laboratories dealing with biological samples or hazardous chemicals. For example, clean areas should be separate from areas handling waste, and high-traffic zones should not interfere with sensitive research stations.
3. Ensure Proper Ventilation and Safety
Ventilation is a critical factor in laboratory design, particularly when dealing with hazardous chemicals, biological samples, or airborne contaminants. Adequate ventilation systems, including fume hoods and air filtration units, must be installed to maintain air quality and prevent exposure to harmful substances. Emergency exits should be strategically placed for quick evacuation in case of an incident. Fire suppression systems, such as sprinkler systems and fire extinguishers, should be readily available, and laboratories must comply with local fire safety regulations. Ultimately, proper ventilation and safety mechanisms reduce risks and create a secure working environment.
4. Plan for Equipment and Storage
Proper storage and equipment placement are essential for a well-functioning laboratory. Each piece of equipment should have a designated area that allows for ease of use and maintenance. Storage areas should be designed to accommodate chemicals, biological samples, and laboratory tools while securing compliance with safety regulations. Flammable and hazardous materials must be stored in specialised containment units to prevent spills and contamination. Additionally, laboratory furniture should be selected to support ergonomic and efficient work practices, ensuring that researchers can access necessary materials with ease.
5. Consider Ergonomics and Accessibility
Ergonomics play a significant role in laboratory design, influencing comfort, efficiency, and safety. Workbenches and equipment should be positioned at appropriate heights to reduce strain on workers. Seating arrangements should support long hours of research without causing discomfort. Accessibility is another crucial factor so that pathways are clear and workstations are easy to navigate. Laboratory spaces should comply with accessibility regulations, allowing disabled individuals to move freely and operate equipment without hindrance. A well-designed laboratory prioritises user comfort while maintaining a functional and safe workspace.
Best Practice Tips for Designing a Laboratory Layout
Maximise Flexibility
Laboratories should be designed with adaptability in mind. Using modular furniture and movable workstations allows facilities to reconfigure spaces as research needs evolve. This flexibility makes sure that the laboratory remains functional even when equipment or staffing requirements change.
Prioritise Safety
Safety should be the foremost concern in laboratory design. Zoning hazardous and non-hazardous areas effectively reduces contamination risks. Implementing clear safety protocols, signage, and easy access to emergency exits means that staff are protected in case of incidents.
Enhance Workflow Efficiency
Optimising workflow reduces bottlenecks and improves productivity. Minimising the distance between frequently used equipment, ensuring logical work sequences, and organising tools efficiently contributes to a smoother research process. Creating dedicated work zones for specific tasks further enhances efficiency.
Ensure Compliance with Regulations
Regularly reviewing and adhering to safety and regulatory guidelines is critical for maintaining a compliant laboratory. Compliance audits, periodic safety checks, and up-to-date documentation on safety procedures help laboratories avoid penalties and ensure a secure working environment.
Incorporate Smart Technology
Integrating automation and digital monitoring enhances laboratory management. Smart technology can help track inventory, monitor equipment conditions, and optimise resource usage. Implementing digital documentation and cloud-based tracking systems improves accessibility and efficiency.
Advanced Best Practices for Laboratory Design
- Invest in Advanced Safety Features: Implement real-time air monitoring systems and digital hazard alert mechanisms to detect chemical spills, gas leaks, or fluctuations in air quality. Automated alerts allow for immediate response, reducing potential risks to personnel.
- Sustainable Design: Implement energy-efficient lighting, smart climate control systems, and water-saving technologies to reduce environmental impact. Laboratories should also explore renewable energy options such as solar panels to reach their long-term sustainability goals.
- Integrated Digital Solutions: Smart lab technologies, including cloud-based data storage and automated experiment tracking, improve research accuracy and efficiency. Digital dashboards provide real-time monitoring of lab equipment, reducing maintenance downtime.
- Customised Workstations: Adaptable workstations support a wide range of research activities by allowing for modular layouts and movable fixtures. Adjustable furniture and reconfigurable lab benches enhance workflow flexibility and researcher comfort.
- Regular Safety Audits: Conduct periodic safety reviews, including hazard assessments and regulatory compliance checks, to proactively address potential risks. Updating laboratory protocols based on audit findings helps maintain a culture of safety and continuous improvement.
Expert Guidance from Restore Harrow Green
Planning and designing a laboratory space requires expertise in spatial planning, safety compliance, and future-proofing. Restore Harrow Green provides specialist workplace consultancy and laboratory relocation services to help optimise laboratory efficiency.For expert support in laboratory design and relocation, contact Restore Harrow Green today.