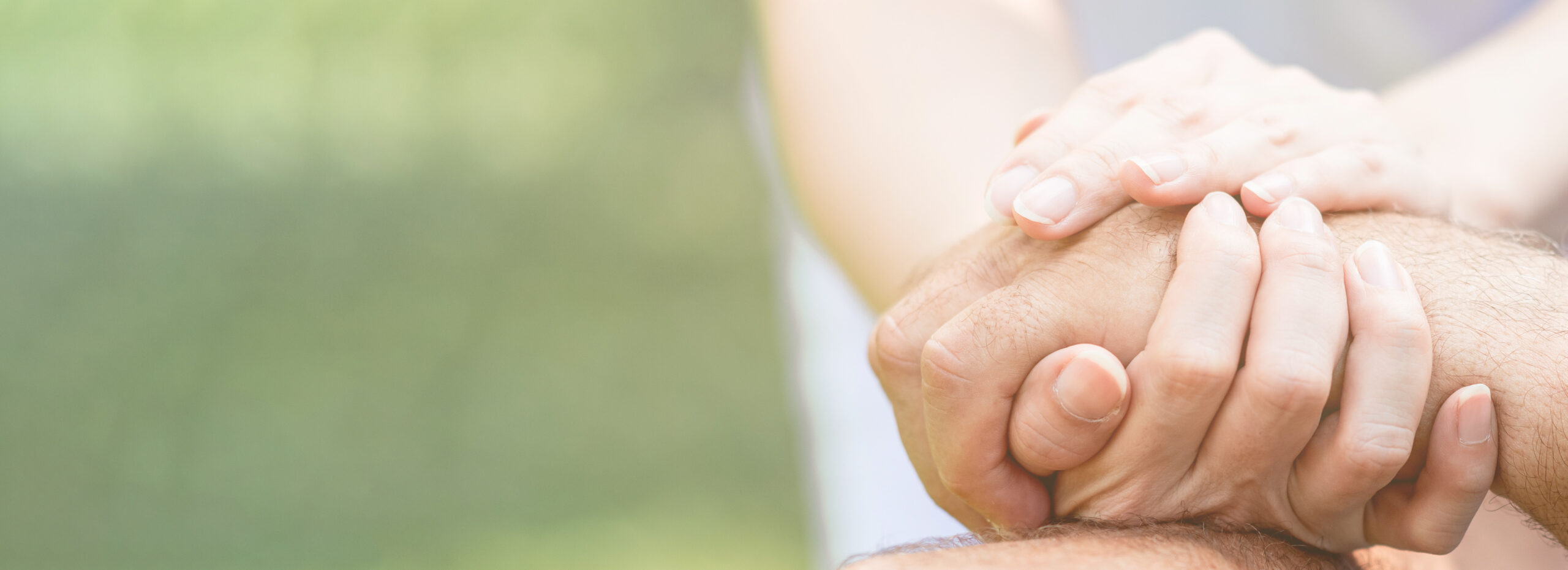
The customer
For fast-food retailer, everything needs to move fast. From the moment a customer places an order to when it’s served, every second counts. But behind the scenes, their Accounts Payable team was stuck in a slow-moving process, juggling thousands of purchase orders, invoices, and supplier requests from their restaurants. All in a system that had become too complex to handle their growing business.
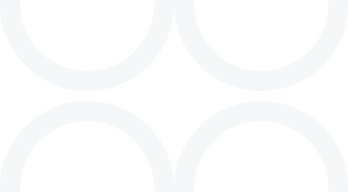
A key member of the AP team, knew something had to change. The system they had relied on for years had outgrown its original design. Workflows had been patched together over time, creating inefficiencies that were causing delays, unnecessary manual work, and supplier frustrations.
Purchase orders, supplier onboarding, and invoice approvals were all managed through a single, tangled workflow that made even small changes difficult. What once seemed like a convenient setup had become a bottleneck, slowing down approvals and creating compliance risks.
Raising a purchase order required multiple manual steps, with no built-in calculations or table data. The approval process dragged on, creating frustration for the AP team and suppliers alike. The team was also struggling with supplier onboarding, which lacked an organised workflow. Bringing on new vendors required a mix of emails, spreadsheets, and back-and-forth follow-ups, creating delays and inefficiencies.
The original system had served them well but as they expanded, they needed something more structured, more automated, and less of a headache.
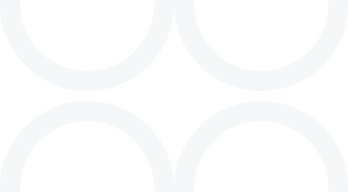
Serving up a new process
With a growing volume of purchase orders and invoices, we rebuilt their workflows from the ground up. Instead of forcing everything through one overcomplicated workflow, they designed dedicated processes for purchase orders, supplier onboarding, and invoice approvals—each one optimised for efficiency.
The new purchase order system introduced advanced forms, which included automatic calculations and structured data, eliminating the need for manual work. Supplier onboarding was revamped with an online submission process, reducing errors and speeding up approvals. Each workflow was built to scale, ensuring that as the company grows, their AP system can grow with them.
“The new system made everything so much smoother. Purchase orders are easier to manage, and our supplier onboarding process is finally structured and efficient.” AP Team
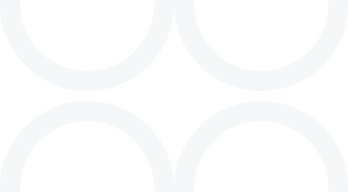
Our customer now processes around 39,000 invoices annually, a clear sign of the system’s ability to handle high volumes with ease. The integration with SAP ensures that supplier information and invoice amounts are automatically updated, reducing the risk of errors. Across multiple locations, 420 employees now use the workflow system to keep operations running smoothly.
“We process tens of thousands of invoices each year. Having a system that integrates with SAP and scales with us is a game-changer.” AP Team
If your AP process is still stuck in manual mode, it might be time for a fresh approach. Our AP processing could be the missing ingredient in your workforce.